abs塑料顆粒的生產(chǎn)工藝主要圍繞三種單體(丙烯腈、丁二烯、苯乙烯)的共聚反應(yīng)展開,根據(jù)聚合方式和流程的不同,常見工藝可分為以下幾類,各有其特點(diǎn)和適用場景:
?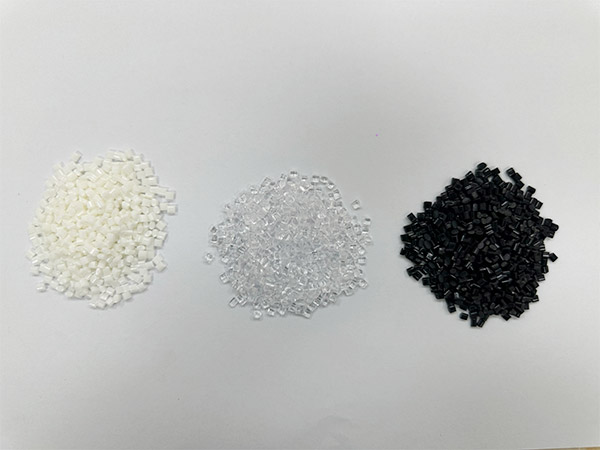
一、乳液聚合工藝
乳液聚合是 ABS 生產(chǎn)中最早工業(yè)化的工藝,也是目前應(yīng)用最廣泛的方法之一,核心是在水介質(zhì)中通過乳化劑使單體形成乳液并發(fā)生聚合反應(yīng)。
工藝流程:
種子乳液制備:先將丁二烯單體在乳化劑(如脂肪酸鈉)作用下分散成乳液,加入引發(fā)劑(如過硫酸鉀),在 50-70℃下聚合形成聚丁二烯(PB)膠乳(粒徑 0.1-0.5μm),作為 “種子”。
接枝共聚:向 PB 膠乳中加入丙烯腈和苯乙烯單體,在 80-100℃下進(jìn)行接枝聚合,使兩種單體在 PB 分子鏈上接枝,形成 ABS 接枝膠乳(含 PB 橡膠相和接枝的 SAN 樹脂相)。
SAN 樹脂制備:單獨(dú)將丙烯腈和苯乙烯按比例共聚,形成苯乙烯 - 丙烯腈共聚物(SAN 樹脂)膠乳,作為連續(xù)相。
混合與凝聚:將接枝膠乳與 SAN 膠乳按比例混合,加入電解質(zhì)(如氯化鈣)破壞乳液穩(wěn)定性,使聚合物凝聚成顆粒。
后處理:凝聚后的顆粒經(jīng)洗滌(去除乳化劑和電解質(zhì))、脫水、干燥,再通過熔融擠出造粒,得到 ABS 顆粒。
特點(diǎn):
產(chǎn)品中橡膠相(PB)分散均勻,沖擊強(qiáng)度高,尤其低溫抗沖性能優(yōu)異;
可精確控制橡膠粒徑(0.1-1μm),適合生產(chǎn)高抗沖級 ABS;
流程較復(fù)雜,成本較高,適合高端制品(如電子外殼、汽車內(nèi)飾)。
二、本體聚合工藝
本體聚合是在無溶劑或少量溶劑的條件下,直接通過單體熔融狀態(tài)聚合,流程更簡潔,成本較低。
工藝流程:
預(yù)聚合:將丁二烯、丙烯腈、苯乙烯按比例混合,加入引發(fā)劑(如過氧化苯甲酰),在反應(yīng)釜中 80-120℃下預(yù)聚合,形成轉(zhuǎn)化率 20%-30% 的粘稠液體。
連續(xù)聚合:將預(yù)聚體送入塔式反應(yīng)器,在 120-180℃下繼續(xù)聚合,轉(zhuǎn)化率提升至 90% 以上,形成高分子量的 ABS 樹脂熔體。
脫揮與造粒:熔體經(jīng)螺桿擠出機(jī)脫除未反應(yīng)的單體(通過真空脫揮),然后冷卻、切粒,得到 ABS 顆粒。
特點(diǎn):
無需乳化劑和凝聚步驟,工藝簡單,生產(chǎn)效率高,成本比乳液法低 10%-20%;
產(chǎn)品純度高,透明性略好,但橡膠相分散不如乳液法均勻,沖擊強(qiáng)度稍低;
適合生產(chǎn)通用級 ABS,多用于對成本敏感的領(lǐng)域(如日用品、包裝材料)。
三、本體 - 乳液接枝聚合工藝(復(fù)合工藝)
為結(jié)合兩種工藝的優(yōu)勢,部分廠家采用 “本體 - 乳液復(fù)合工藝”,流程如下:
先通過乳液聚合制備 PB 膠乳,并接枝丙烯腈和苯乙烯,得到接枝膠乳;
單獨(dú)通過本體聚合制備 SAN 樹脂;
將接枝膠乳與 SAN 樹脂在熔融狀態(tài)下混合、擠出造粒。
特點(diǎn):
兼顧乳液法的高抗沖性(橡膠相分散好)和本體法的低成本(減少乳液后處理步驟);
產(chǎn)品性能均衡,應(yīng)用范圍廣,是目前主流工藝之一。